- 147
- 1
Now for the bearings.
Rod bearings. 8 sets.
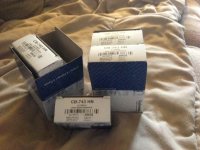
Main bearings.
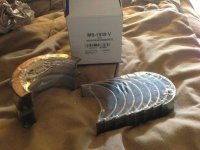
Now on to the piston box.
Mahle rings
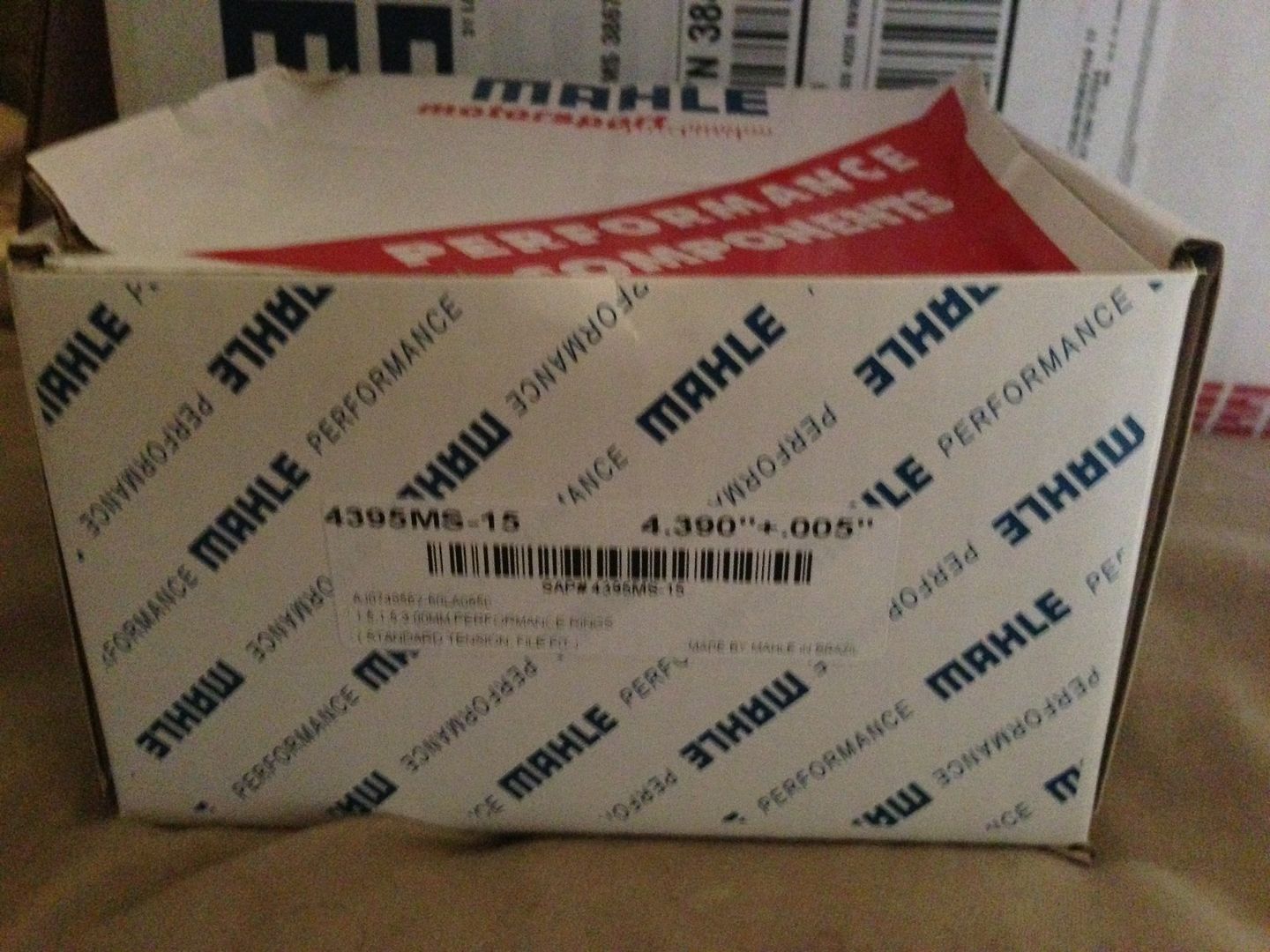
Mahle pins and retainers
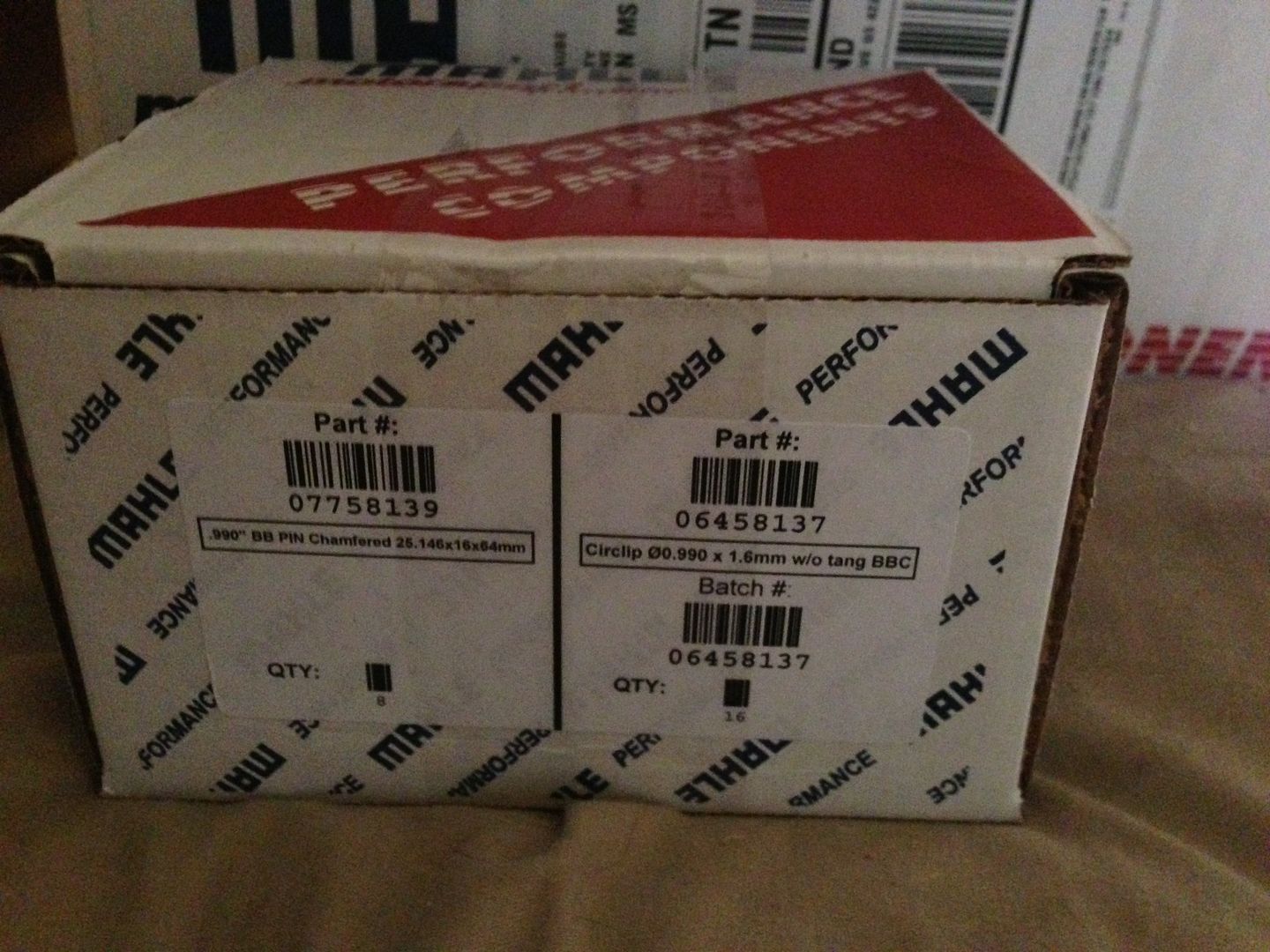
And finally, the Mahle PowerPak pistons
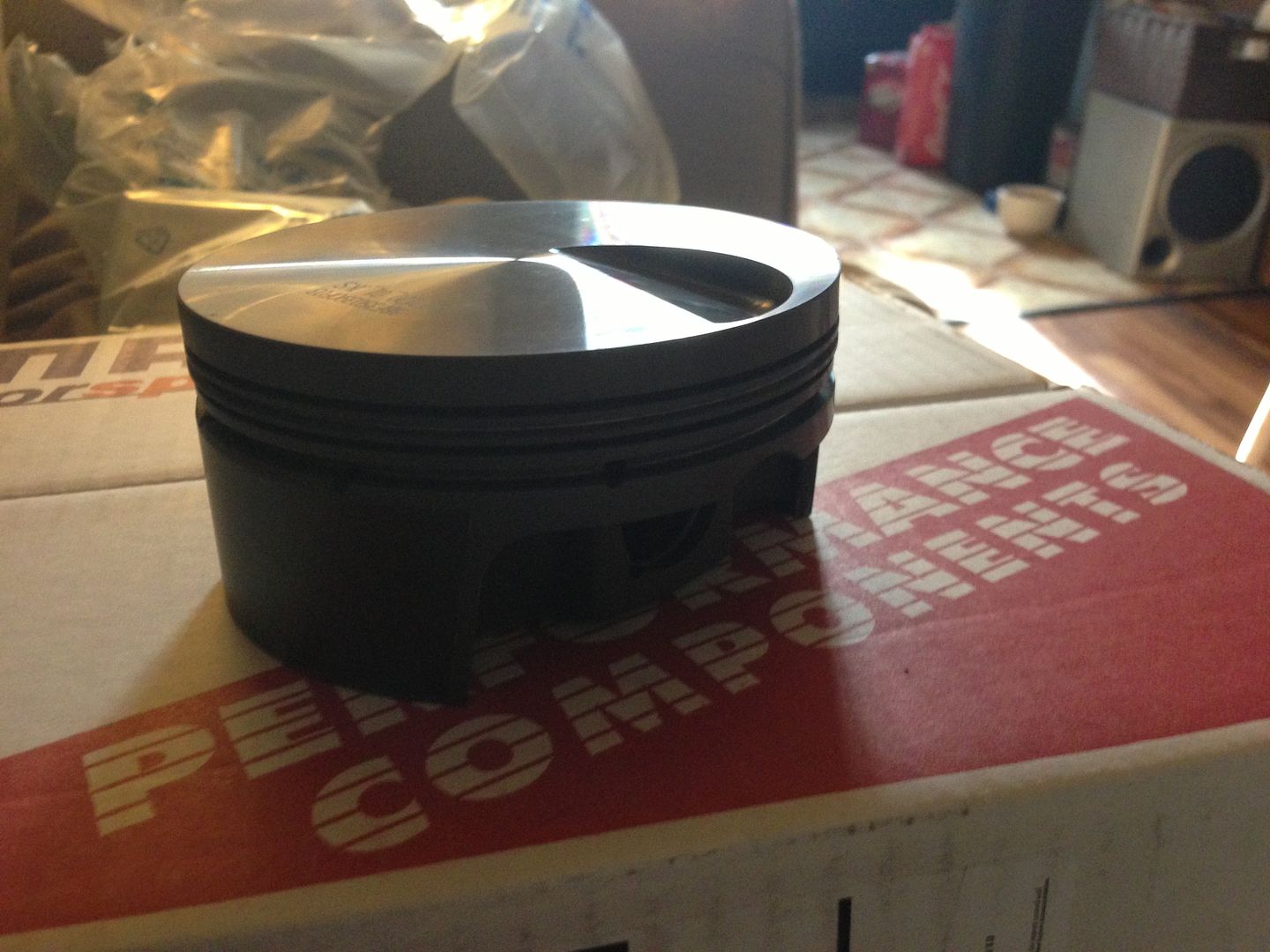
I have to say that this is one beautiful piston. Forged aluminium.
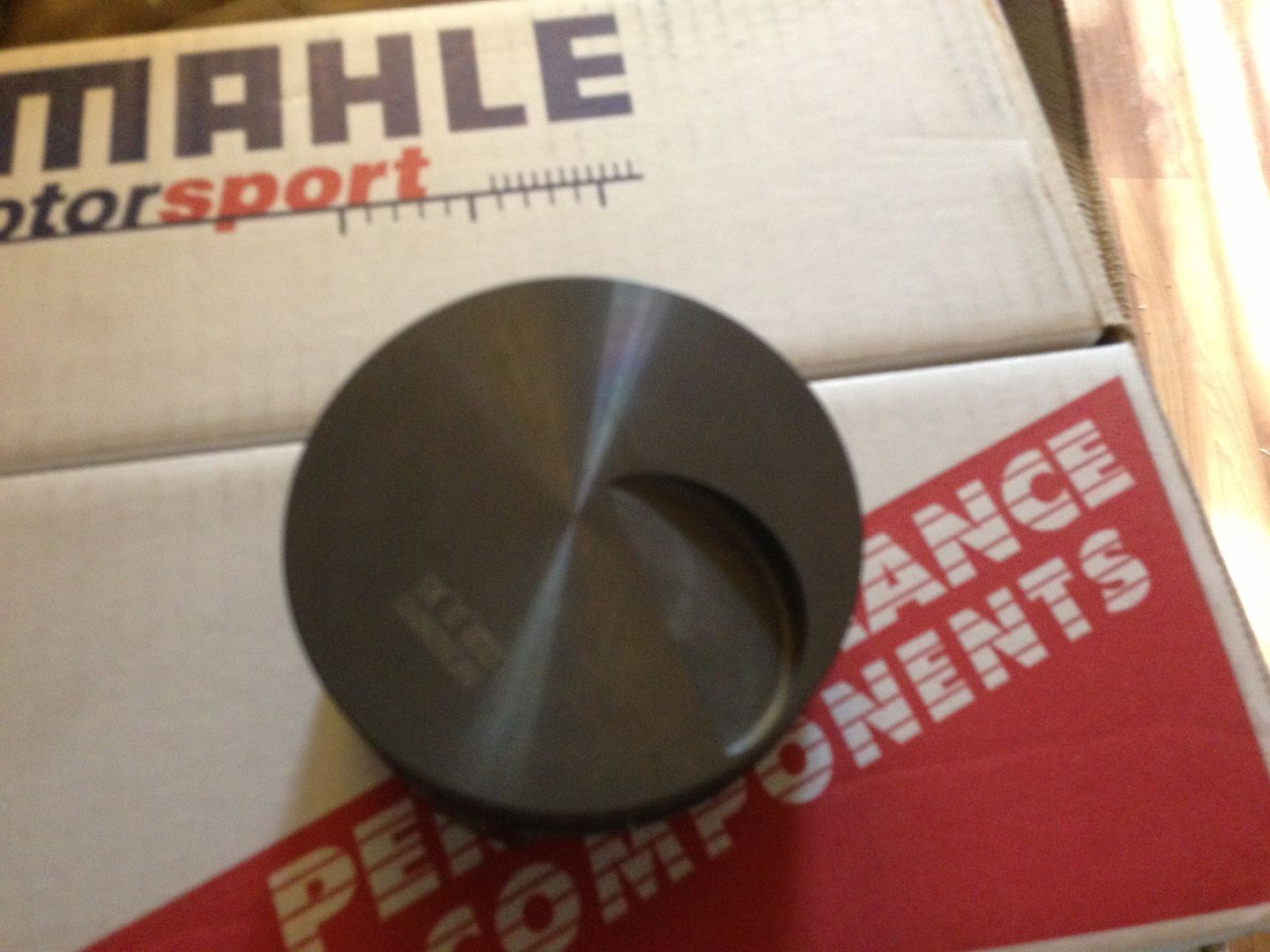
3cc valve relief.
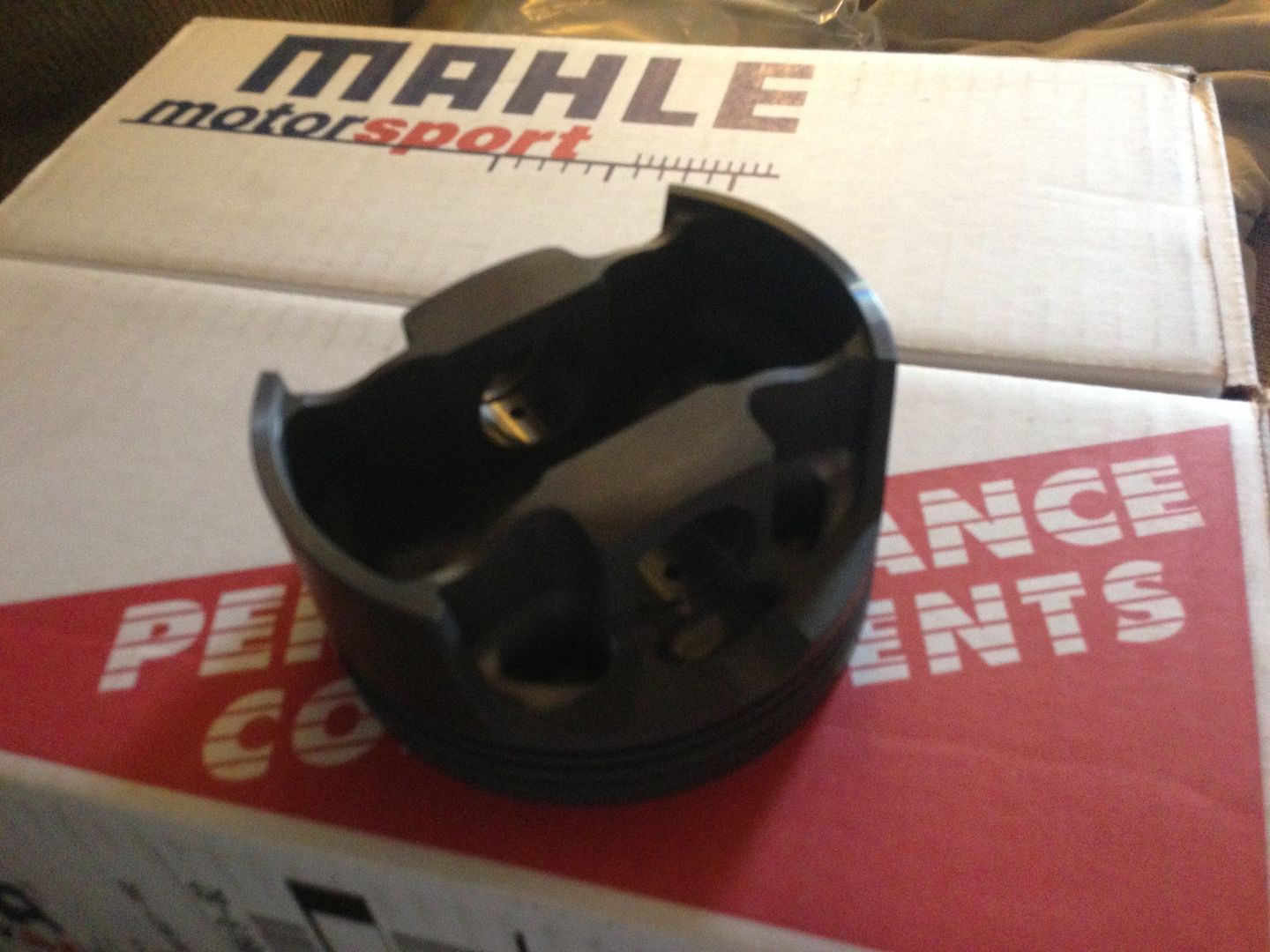
Now the main attraction. The stroker crankshaft.
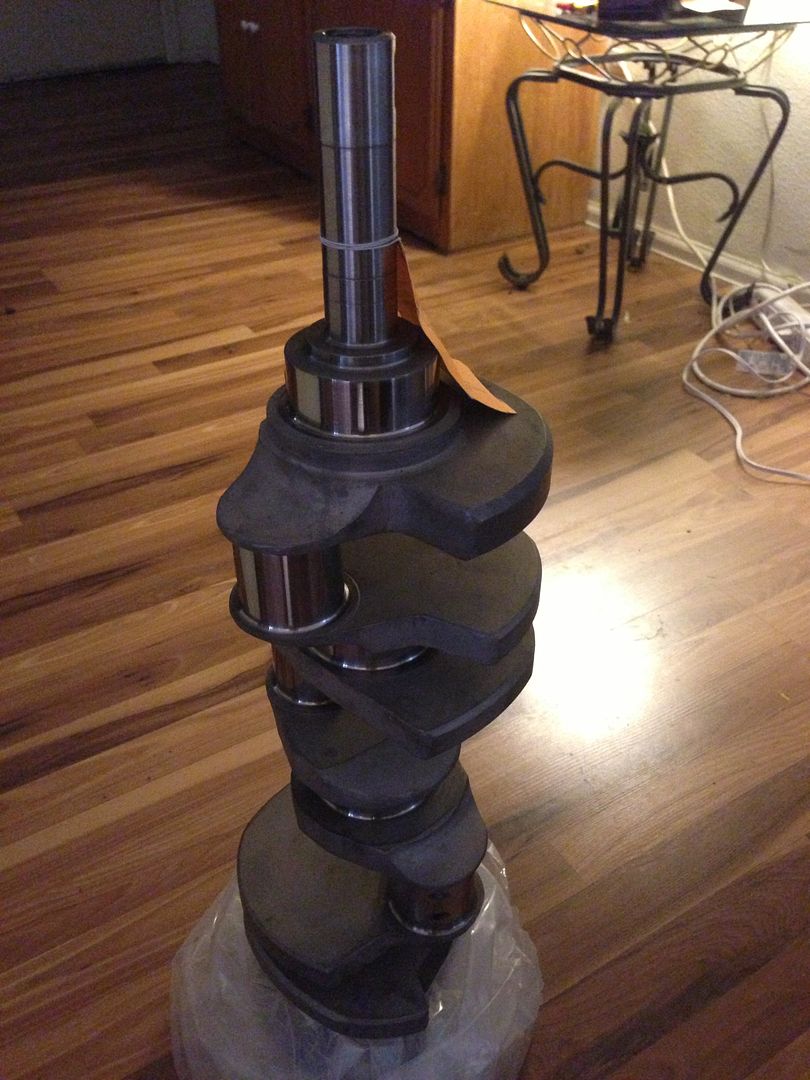
Forged in 4340 steel. This thing weighs a ton!
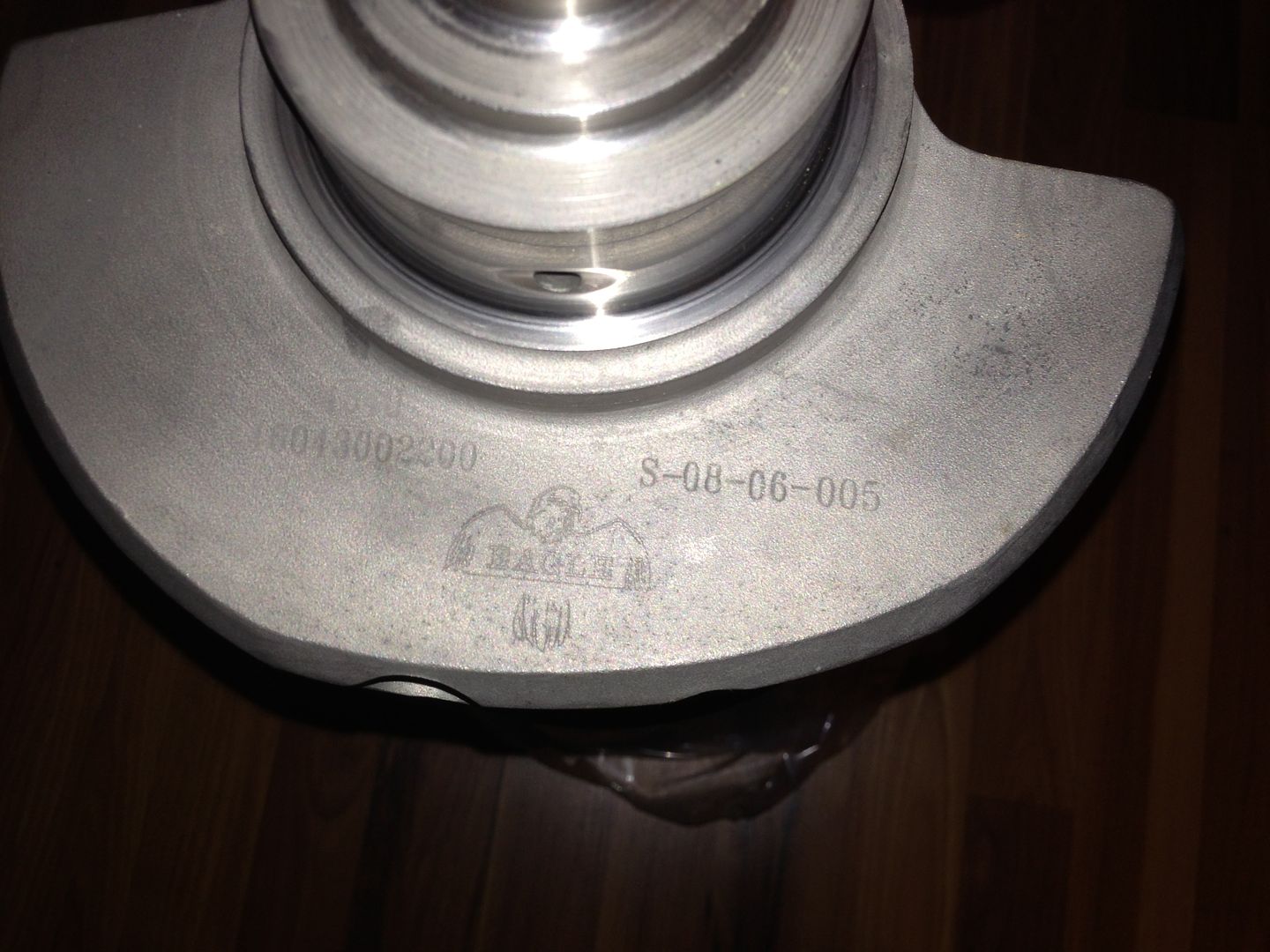
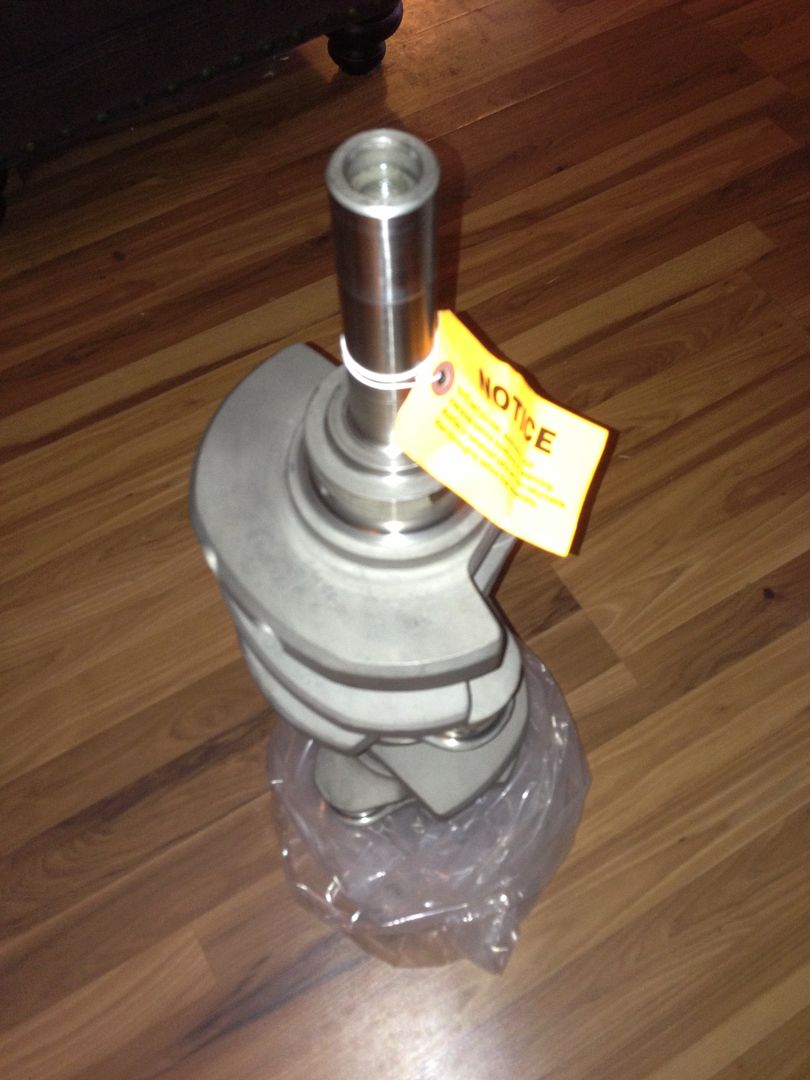
Well that accounts for everything I paid for! I'll be hauling it in tomorrow and probably will be checking bearing clearances in the mains to know if I need to hone more or not. More to come. You know the drill. Stay tuned!
Rod bearings. 8 sets.
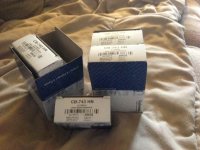
Main bearings.
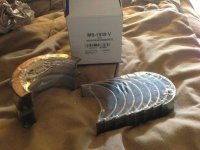
Now on to the piston box.
Mahle rings
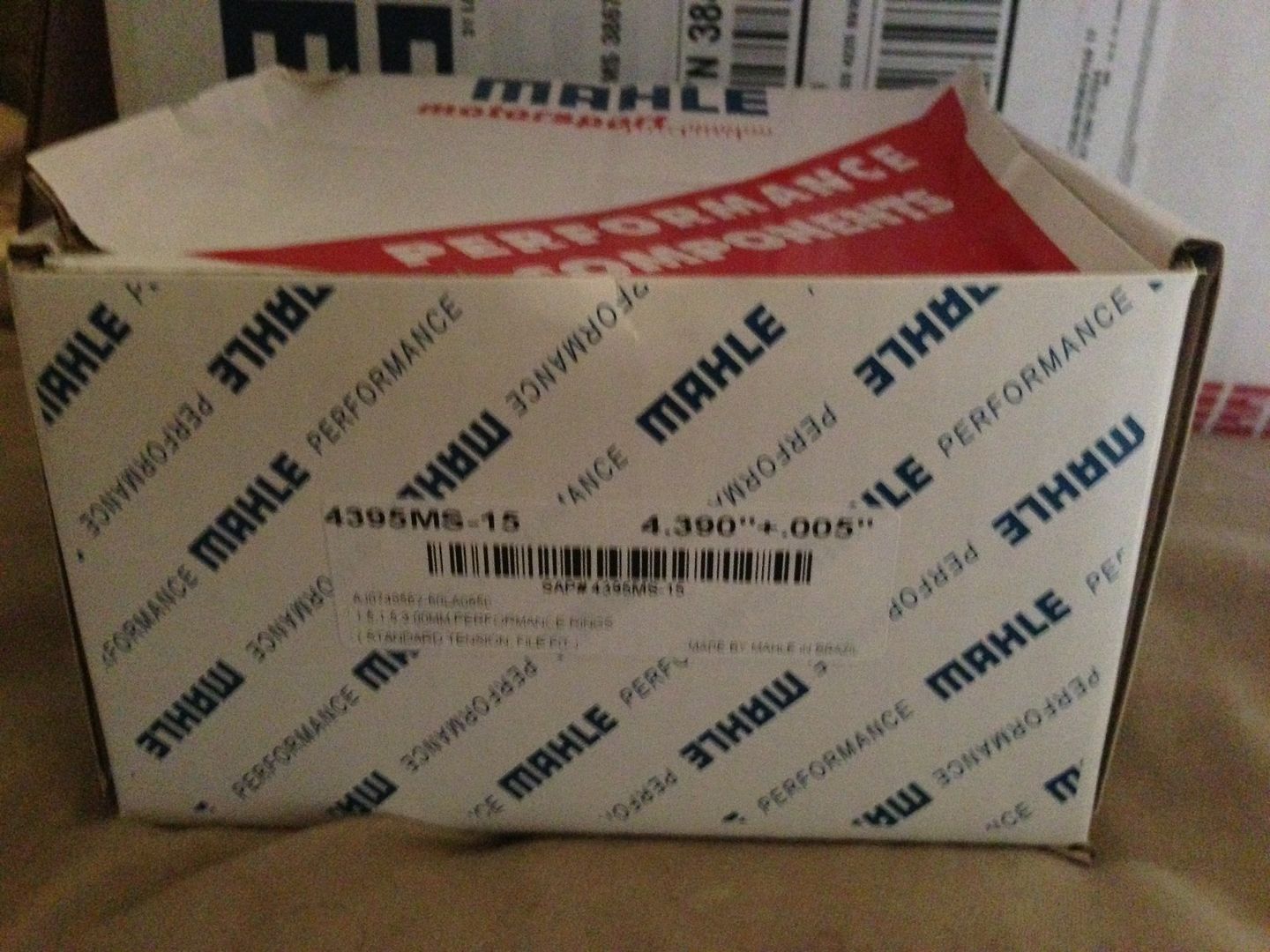
Mahle pins and retainers
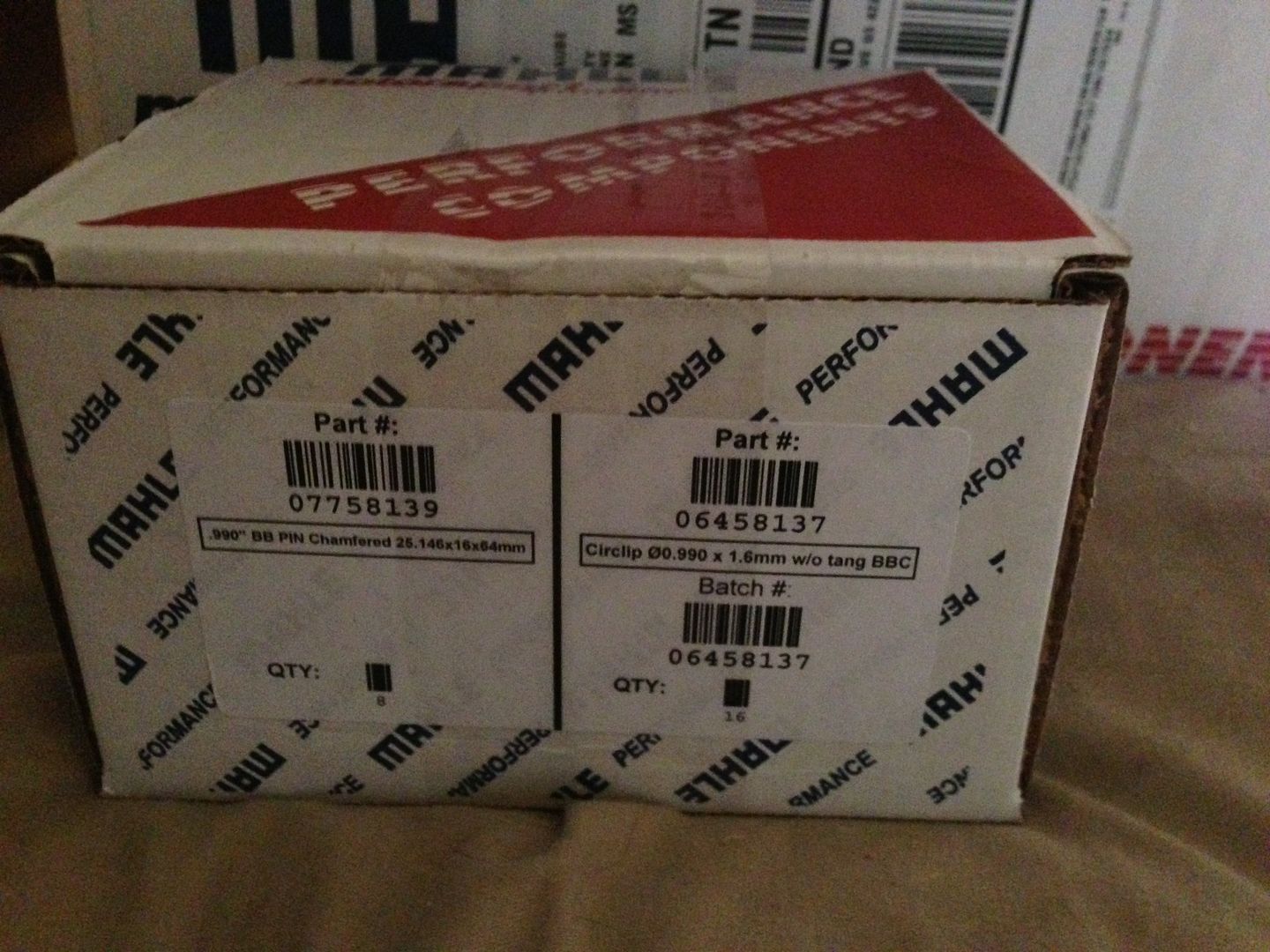
And finally, the Mahle PowerPak pistons
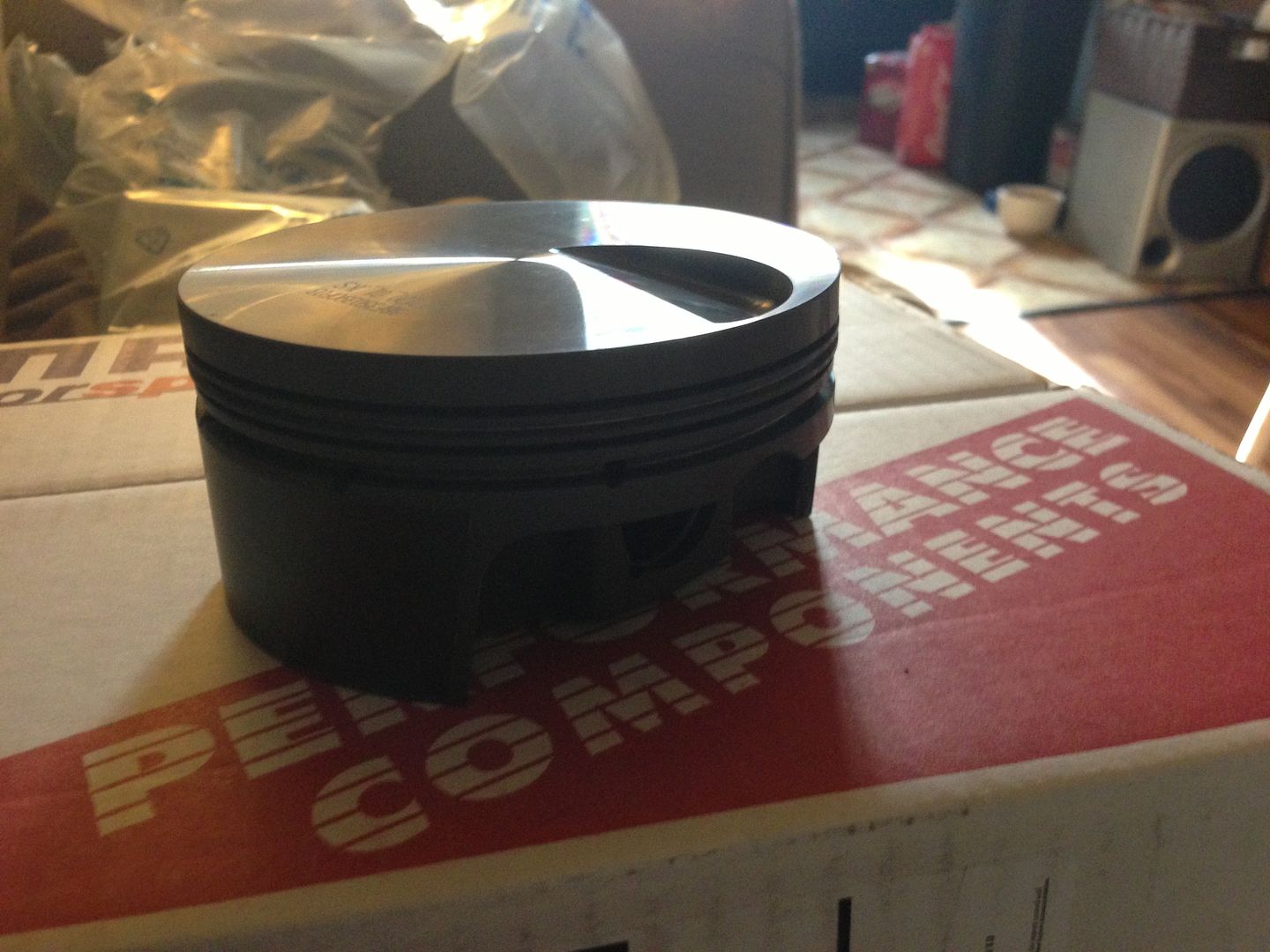
I have to say that this is one beautiful piston. Forged aluminium.
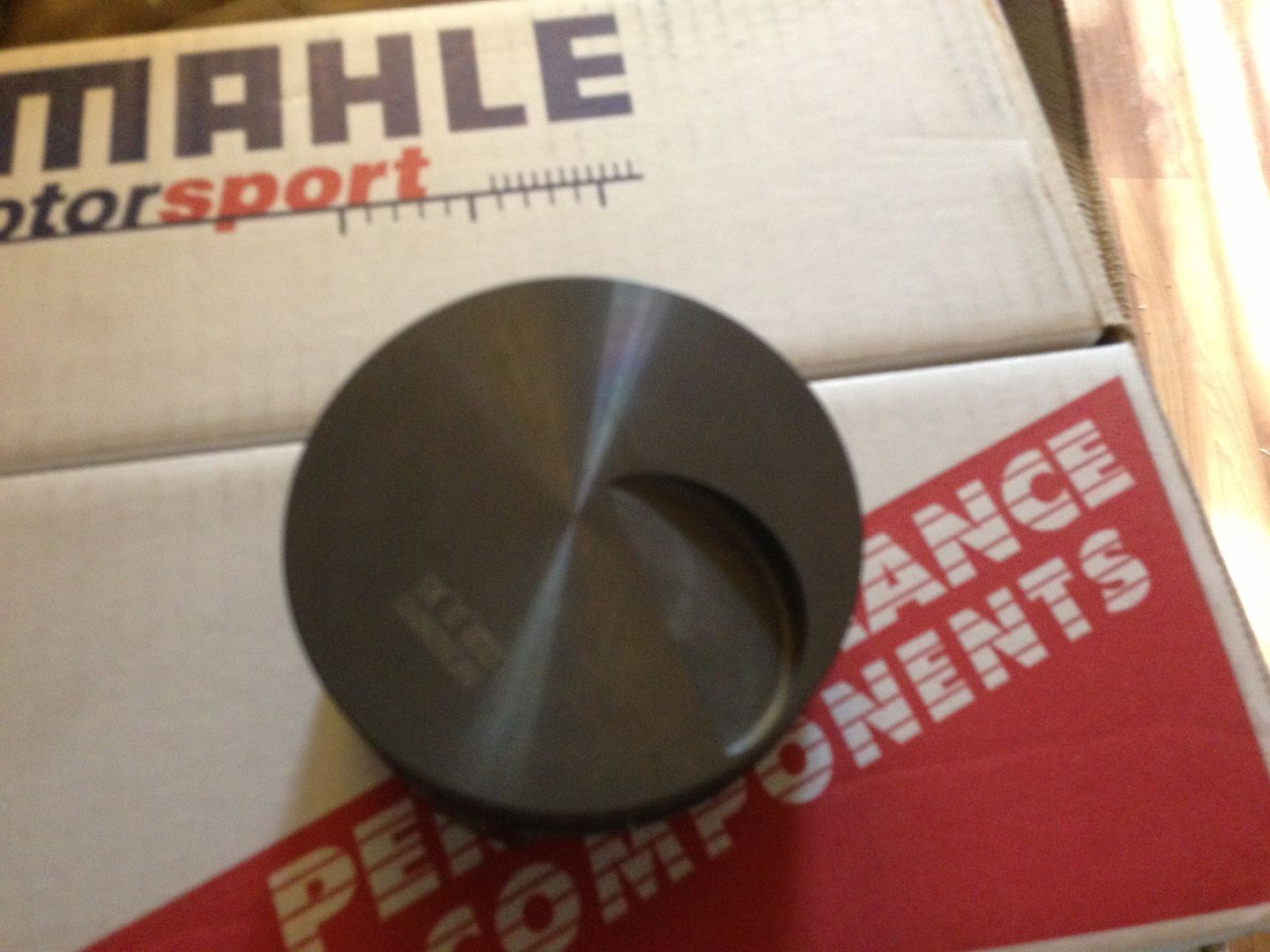
3cc valve relief.
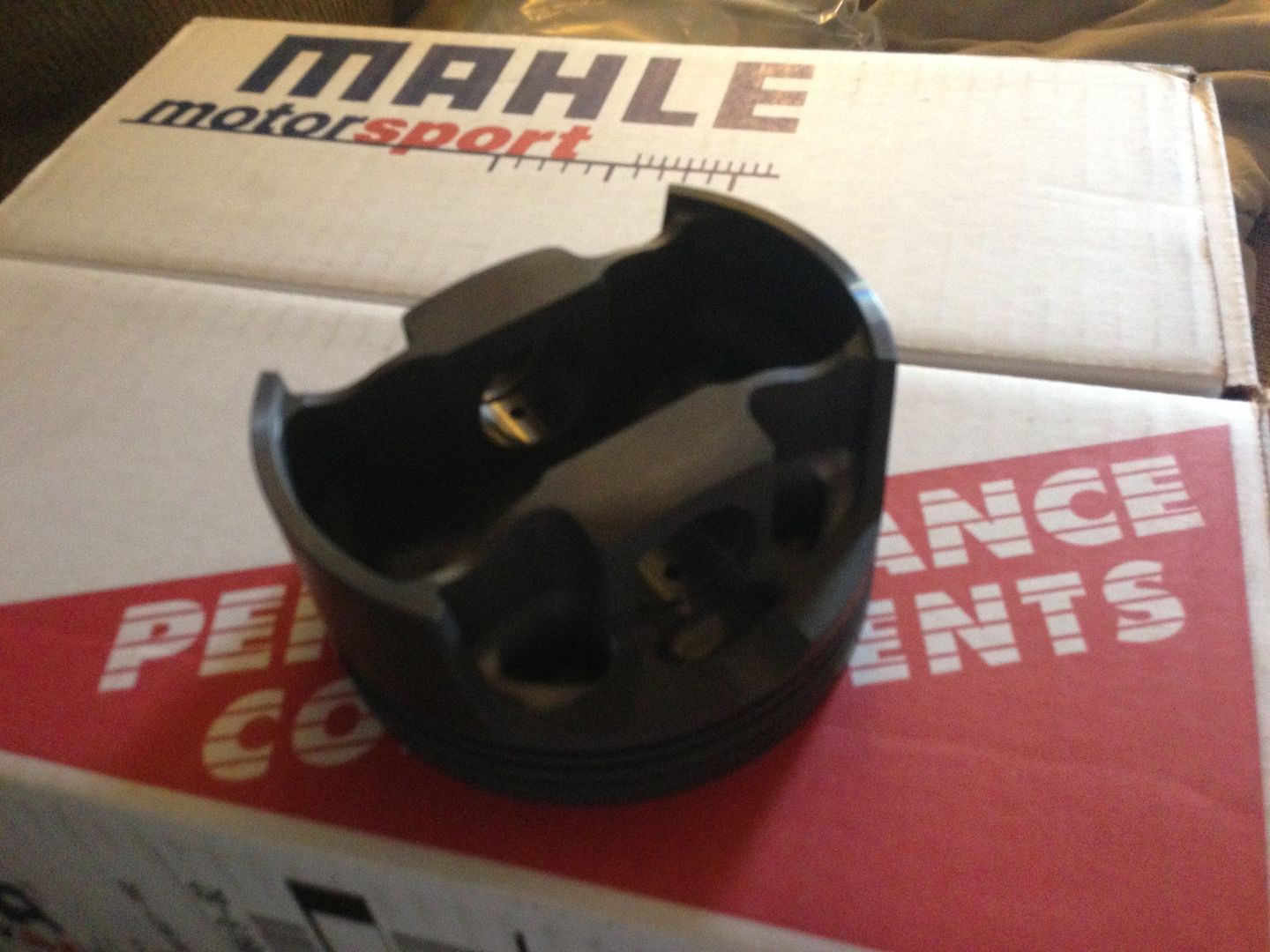
Now the main attraction. The stroker crankshaft.
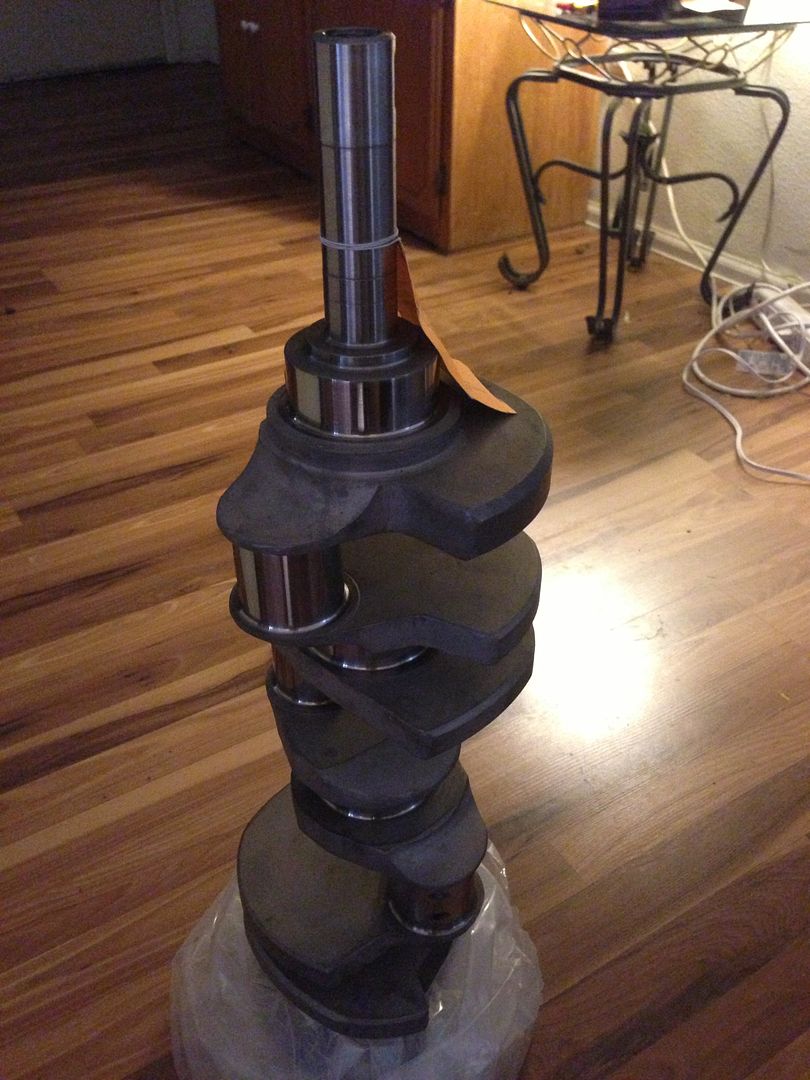
Forged in 4340 steel. This thing weighs a ton!
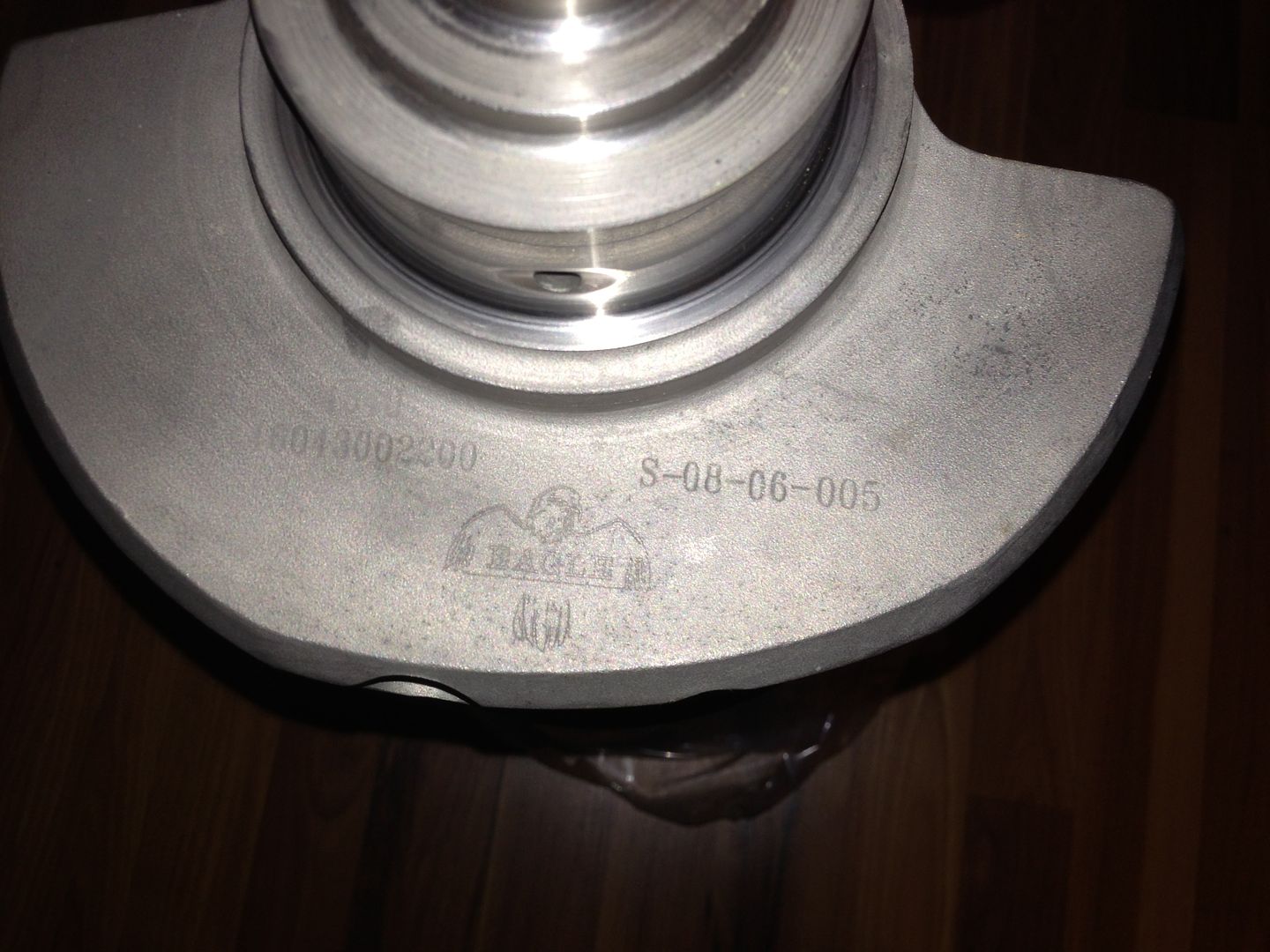
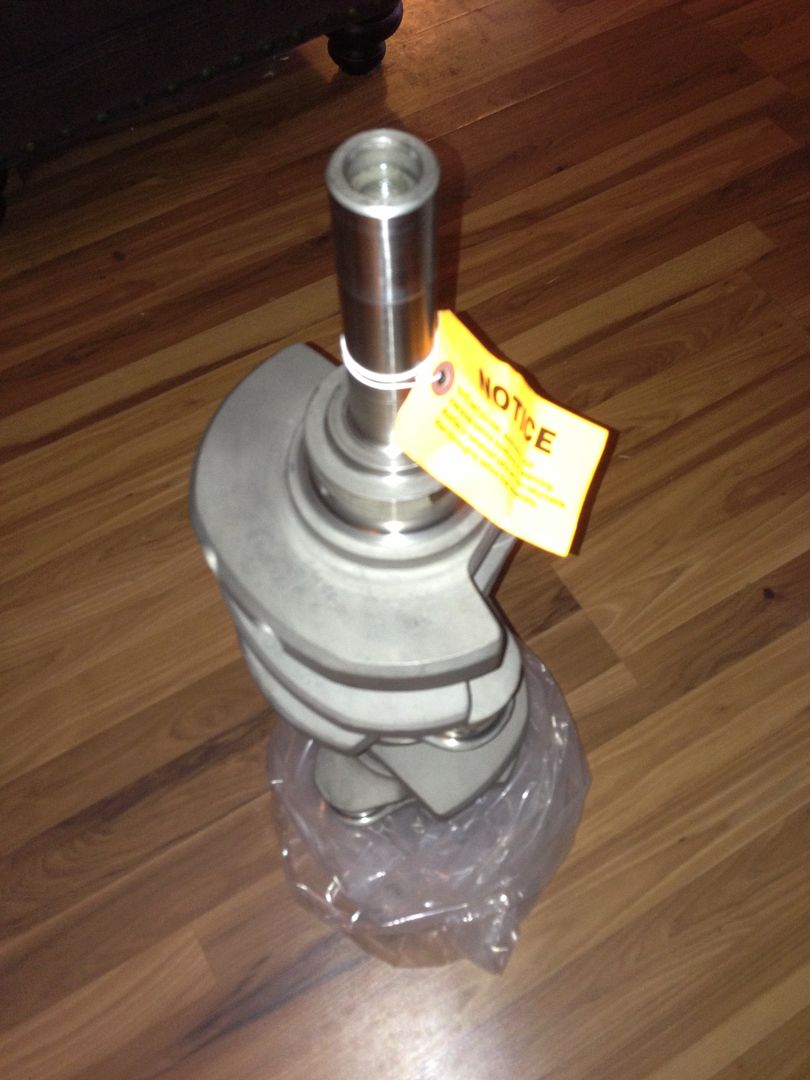
Well that accounts for everything I paid for! I'll be hauling it in tomorrow and probably will be checking bearing clearances in the mains to know if I need to hone more or not. More to come. You know the drill. Stay tuned!